尽管我国钨资源占全球的60%左右,但就其硬质合金的质量来说,与世界领先企业相比,仍然还有相当大的差距。因此,不要说国外,就是在国内的高端硬质合金尤其是数控刀片的需求企业,一般都不会选择本国的产品。 几十年来,国内硬质合金人也进行了不懈的努力和探索。尤其是最近十几年,随着硬质合金制造设备的提升和工艺的改进,使传统硬质合金刀片的品质得到了大大提升。然而,由于影响硬质合金质量的一些致命瓶颈没有突破,因此,国内硬质合金刀片仍然只能徘徊于中低档之间。 究竟是哪些因素影响了我国硬质合金刀片的质量提升呢?这里面固然有工艺控制、精加精度、涂层水平、管理细节等方面的原因,但我认为其最大原因莫过于原材料的先天不足,也就是材料研究学术界流行的一句话叫做“遗传缺陷”。 关于“遗传缺陷”的问题,不只是硬质合金行业存在,它同样存在于各行各业的高端终端产品的制造中。那么,目前影响硬质合金刀片质量提升的最大“遗传缺陷”是什么呢?我想首当为钨钛固溶体及其钽铌添加物的晶貌、细化和均质的问题。 一、 钨钛固溶体 1.固溶体的晶貌 我们知道,钨钛固溶体的钛主要来自于符合冶金要求的钛白粉。其生产工艺为:先将钛白粉、碳化钨和炭黑在混料器中混合均匀,然后卸料进行打舟,将打好的舟放入碳化炉中高温烧结,或者,装舟放在真空炉中烧结。其化学反应式为:TiO2+WC+C—(Ti+W)C+CO↑。从这一反应式可知,首先,在高温状态下,炭黑先将钛白粉中的氧还原掉,然后,剩余的碳再与钛结合成碳化钛。而在热力学的驱动下,以错位的方式,钨的质点不断占据钛的点阵位置而形成置换式固溶或者叫点阵式固溶,从而,得到我们需要的钨钛固溶体。 从上述简单描述的固溶过程来看,由于钛白粉中的氧形成CO跑掉以后,会留下一定的空间,而固溶又是以错位方式来完成的。因此,就必然会造成钛钨质点挨得近的固溶得快,远的则固溶得慢。并且,挨得远的需要不断的延长时间和吸收能量才行。否则,就会因固溶度不够而形成非单相固溶体。然而,挨得近的钛钨质点固溶好了以后,在能量不断供给的情况下就会不停地聚集而形成粗晶,而钨钛质点隔得较远的则会形成相对较细的晶粒。因此,这样条件下形成的固溶体晶貌肯定会不完整。为此,本人经过长期的研究和实验,通过改变传统的生产工艺,现已基本解决了钨钛固溶体晶貌不完整的问题(见图)
 传统真空炉生产的钨钛固溶体(FSSS1.26微米)
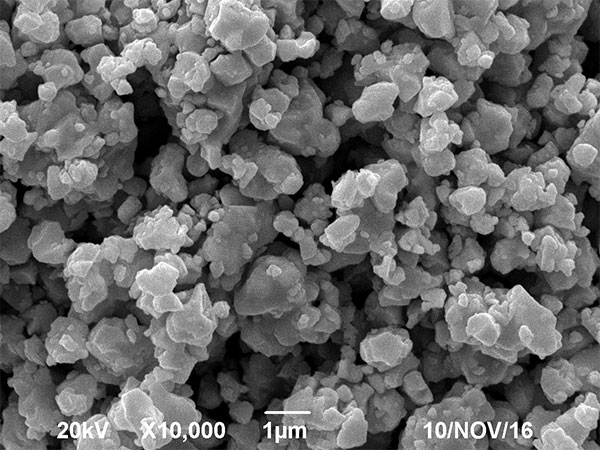 新兴工艺生产钨钛固溶体(FSSS0.90微米)
从放大10000倍的电镜图可以看出,传统工艺中,尽管我们采用了真空炉,生产出来的固溶体仍然没有完整的晶貌(碳管炉生产的更差),晶粒边缘不清晰,形态不规整。而采用新兴工艺生产出来的固溶体则不论晶形晶貌还是粒度的均匀性方面都要好得多。那么,采用新兴工艺生产出来的固溶体做原料来生产硬质合金,其质量指标有何提高呢?根据本人在2012年9月所做的一组实验数据可以说明这一问题。当时,我以新兴工艺生产的中颗粒固溶体(当时还没有掌握生产超细颗粒的技术)配置了一公斤的YT14混合料,并添加了0.45%的TaC,其余均按YT14硬质合金的工艺生产了15根实验条。选了其中10根较规整的做了几项性能指标,其密度、强度、硬度指标如下: 密 度 (g/mm3) 抗弯强度(kn/mm2 ) 硬 度(HRA) 1、 11.58 1780 91.3 2、 11.62 1710 91.5 3、 11.55 1660 90.9 4、 11.60 1790 91.1 5、 11.56 1770 91.2 6、 11.61 1760 91.2 7、 11.57 1820 90.8 8、 11.53 1550 91.4 9、 11.59 1830 91.3 10、 11.61 1810 91.4
从这一组数据分析来看,除合金的密度只是稍微比标准的YT14大一丁点外,其强度和硬度均有较大幅度的提高。 2.固溶体的粒度 为满足制造业不断向前发展的需要,不论是粉末冶金方式成型还是铸造成型,不论是晶体结构还是玻璃体结构,都对前期原材料的品质提出了越来越高的要求。其中,最迫切的要求是对原材料粉末粒度的不断细化。 前已述及,硬质合金中的钛是从TiO2中得来。而TiO2又是一个稳定性较好的金属氧化物,要还原掉它的氧必须是在高温下以碳还原方式才行(真空炉需要1600度左右,碳管炉则需1800度左右)。而在如此高的温度下形成的钛粉微粒活性很高,可迅速与碳结合形成TiC粉末,形成的TiC粉末又迅速聚集形成较粗颗粒的TiC。因此,利用传统的碳化工艺根本无法生产超细和接近纳米颗粒的TiC粉末和相应的固溶体。 为了得到超细颗粒的钨钛固溶体,个别厂家先利用真空炉生产出1.5微米左右的固溶体,再用湿磨机进行强化球磨100个小时以上。这样虽然也可以得到超细的钨钛固溶体,但其性能远远达不到新兴工艺直接生产出来的超细钨钛固溶体。这是因为: ① 粉末粒度的记忆效应难以消除。 我们知道,同种粉末粒度的大小是与粉末粒子所蕴藏的内能和表面能直接相关的,粒度大说明所蕴藏的能量高。而将较粗的粉末进行强化球磨很大程度上只能消除其外表的畸变能和松散团粒间的应力能,很难消除细晶间的结合能。也就是说,要消除粉末粒子所蕴藏的能量是很难的。而粉末保存了能量就相当于保存了原有粒度的记忆。在合金制作过程中,这些看似变小了的粒子在高温下又会迅速变大。国外有人做过实验,将普通细颗粒YG合金混合料通过湿磨使其达到超细颗粒的粒度效果,至少要湿磨120小时以上,而YT合金则要140小时以上。 ② 合金夹粗严重且杂质含量高。 由于湿磨时间过长,造成大量合金球和球磨桶壁被磨掉而混入了合金原料中。我们先不管湿磨用的合金球是用什么材料做的,由于被磨掉后进入料中的合金球是已经合金化了的,其粉末是WC和Co的固溶体颗粒。因此,即使合金球是用纳米级材料做成,而在第二次的合金烧结过程中仍然会迅速长成较粗颗粒。另外,可倾式球磨机一般都是不锈钢制作的,因此,长时间湿磨也会造成合金原料中铁的成分增加。 ③ 合金原料氧含量大大增加。 由于湿磨时间过长,造成合金粉表面活性增强,从而造成合金粉料在制备过程中极易吸附氧和直接被氧化。 ④ 合金粒度不均匀。 采用强化球磨降低粉末粒度的方法就是将合金球不断冲击和研磨原料,使原料的畸变能和部分团粒间的应力能不断消除的过程。湿磨的前期消除畸变能是比较容易的,但到了后期,由于硬质相粉末的颗粒的外形都基本一致,所以,在机械力的作用下,合金球对各个硬质相粉末团粒所做的功都基本相当。因此,强化球磨不能改观原始粒度的不均匀性。 3.固溶体的均质。 在当代高端材料的研究和应用中,对材质的均匀性问题提到了很高的高度。光是平均粒度细没用,而要均匀的细。套用孔子说的“国患不立,尤患不均”改成“材患不细,尤患不均”再贴切不过了。从前面电镜图可以看出,采用新兴工艺生产的钨钛固溶体粉末的均匀性比用真空炉生产的都强了许多。
二、 钽铌及其它添加物 目前,在硬质合金领域普遍使用的添加物有:碳化钽、碳化铌、钽铌固溶体、碳化钒、碳化铬等。除用Ta2O5做原料生产碳化钽的温度稍高一点外,其余几种所需的还原碳化温度比较低,都比较容易生产出超细的碳化物粉末。而通过两次还原和碳化的过程,碳化钽也能生产出超细颗粒粉末来。
三、 采用新兴工艺生产合金刀片质量提升展望 1.大大延长合金的使用寿命。 不管是晶体结构还是非晶体结构,采用超细和纳米级且均质的原材进行生产,其产品的使用性能都有较大的提高。硬质合金领域,在YG类合金中得到了验证。当合金的碳化钨晶粒接近纳米级时,其合金的强度和硬度均有较大幅度的提升。它颠覆了常规合金强度高硬度就低,硬度高强度就低的一般认知。那么,如果我们采用新兴工艺的钨钛固溶体和超细的添加物生产出来的合金刀片,其强度和硬度也肯定会有较大幅度的提高是不容置疑的。 2.提高合金的精磨精度。 由于合金的晶粒细化了,自然合金的被精磨精度就会提高。 3.增强涂层的附着力(需经验证)。
株洲华斯盛高科材料有限公司 张辅魁 2016年11月10日
|